The question: I’m thinking of buying an old house. It will need a lot of work, and I want to do much of it myself. I’m especially interested in whether the windows can be restored. Any advice?
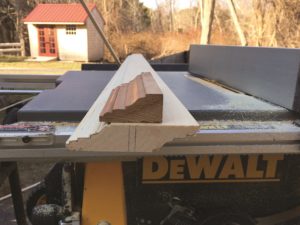
I moved into my partner’s 270-year-old house 18 years ago, and since then, restoring it has been a full-time job. I’ve spent about 10 of those years working on the windows, which were painted over and unusable. In the process of fixing them, I’ve become particularly obsessed with getting the trim right. Preserving the look of an old house takes attention to detail.
Inevitably, not every inch of the old trim can be preserved. I’ve broken the trim trying to get to the glass. In one instance, I lowered a set of windows that were flush against the ceiling. In that case, I needed trim for the top afterwards.
One challenge of restoring an old house is that much of the hardware needed isn’t made anymore. I dig around the house and the shed looking for materials that I can use to replicate the old pieces. The goal is to get a uniform look, but it takes quite a bit of trial and error to figure out what works.
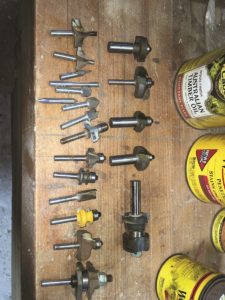
For rebuilding the frames themselves, an important consideration is getting wood to match the look of the old wood. The problem with new wood is that it takes stain differently, and the growth rings are larger than the tighter rings typical in old pine. So, I raid places in the house that nobody will see — like beneath the cabinets. I’ll pull wood from under there and replace it with new plywood. There was also a lot of old wood stacked up in a barn on the property. But I’ve also found good material at the wood and metal pile at the transfer station.
Once I’ve got the wood, the trick is recreating the shape of the old trim. If the new piece of trim will be right up against the old one, it’s important to mimic the shape as closely as possible. I trace the profile of the trim I’m trying to replicate, then figure out the best way to cut it. If the trim is a squared-off cut, I can use the table saw. If it’s a V-cut, I’ll use the router bit. I’m constantly working the ins and outs of every turn and what bits will work. Sometimes I just have to shave the board off at an angle and nibble away at its edge.
A lot of tools are involved: a table saw, miter saw, router bits, some hand planes, chisels, and utility knives. I’ve got quite an assortment of router bits. The detail work is important to getting the grooves as close as possible to the old ones. It’s very time consuming, and I’ve ruined a few boards in the process.
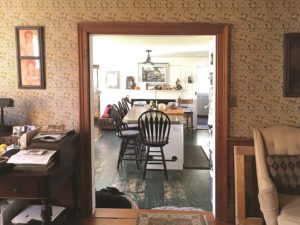
Once I’ve approximated the shape, the next challenge is matching the stain or the paint. Paint is much easier to match; stain is nearly impossible. I’ll look at a piece and try to identify the color tones, whether red, honey, or darker. Then I use eyedroppers to mix in tiny amounts of coloring, recording the amounts so that if I do happen to hit on a fit, I can replicate it.
My trim work may never be perfect, but after a while I get “house blind” to the imperfections and can appreciate the overall effect and effort involved. It’s a labor of love.
This week’s Dovetail Joint question is answered by carpenter Aimée Eckman of Eastham. Keep sending your questions and we’ll find more good answers.